Alcast Company Fundamentals Explained
Table of ContentsAlcast Company for DummiesThe Alcast Company PDFsThe 7-Minute Rule for Alcast CompanyExamine This Report about Alcast CompanyAlcast Company Fundamentals ExplainedThe Facts About Alcast Company Revealed
The subtle difference lies in the chemical web content. Chemical Contrast of Cast Aluminum Alloys Silicon promotes castability by reducing the alloy's melting temperature level and boosting fluidity throughout spreading. It plays a vital duty in allowing elaborate molds to be filled up precisely. Additionally, silicon contributes to the alloy's strength and use resistance, making it valuable in applications where longevity is vital, such as automobile parts and engine elements.It also enhances the machinability of the alloy, making it less complicated to process into finished items. In this means, iron adds to the total workability of aluminum alloys.
Manganese adds to the toughness of aluminum alloys and boosts workability (Foundry). It is frequently made use of in wrought light weight aluminum items like sheets, extrusions, and profiles. The existence of manganese aids in the alloy's formability and resistance to splitting during manufacture processes. Magnesium is a light-weight element that provides stamina and effect resistance to aluminum alloys.
The Best Guide To Alcast Company
It permits the manufacturing of light-weight elements with superb mechanical residential or commercial properties. Zinc enhances the castability of aluminum alloys and assists control the solidification process during spreading. It boosts the alloy's strength and firmness. It is commonly located in applications where intricate shapes and fine details are needed, such as decorative spreadings and certain vehicle parts.
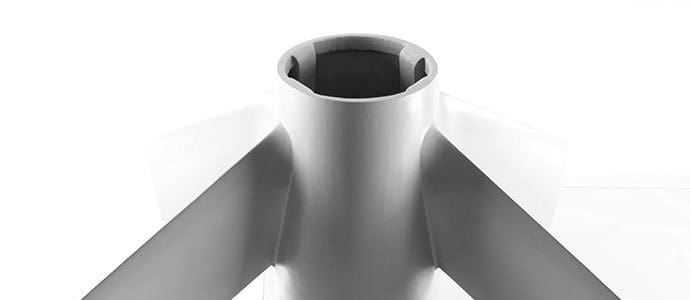
The key thermal conductivity, tensile strength, return strength, and elongation vary. Select ideal raw products according to the efficiency of the target product created. Amongst the above alloys, A356 has the greatest thermal conductivity, and A380 and ADC12 have the most affordable. The tensile restriction is the opposite. A360 has the most effective return strength and the highest prolongation price.
Alcast Company Can Be Fun For Anyone
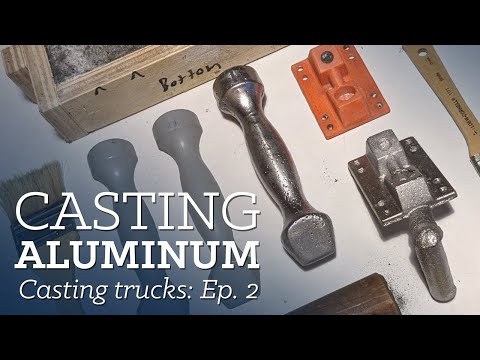
In accuracy casting, 6063 is appropriate for applications where complex geometries and top quality surface coatings are critical. Instances consist of telecommunication enclosures, where the alloy's exceptional formability enables smooth and cosmetically pleasing designs while maintaining structural honesty. Similarly, in the Lighting Solutions industry, precision-cast 6063 elements produce classy and reliable illumination fixtures that need complex forms and excellent thermal performance.
It brings about a finer surface area finish and far better corrosion resistance in A360. Moreover, the A360 exhibits superior prolongation, making it suitable for complicated and thin-walled parts. In accuracy spreading applications, A360 is appropriate for industries such as Consumer Electronic Devices, Telecommunication, and Power Tools. Its boosted fluidness enables complex, high-precision parts like smartphone housings and communication tool housings.
Alcast Company - The Facts
Its distinct buildings make A360 a valuable option resource for accuracy spreading in these sectors, enhancing product sturdiness and high quality. aluminum casting manufacturer. Light weight aluminum alloy 380, or A380, is an extensively made use of casting alloy with several distinct qualities.
In precision casting, light weight aluminum 413 shines in the Consumer Electronics and Power Tools markets. It's generally used to craft intricate components like mobile phone housings, camera bodies, and power tool cases. Its accuracy is impressive, with tight resistances as much as 0.01 mm, making sure flawless item setting up. This alloy's premium rust resistance makes it an outstanding selection for exterior applications, making certain long-lasting, long lasting items in the discussed industries.
Some Known Details About Alcast Company
As soon as you have actually made a decision that the aluminum die casting procedure appropriates for your job, an essential next step is selecting the most suitable alloy. The light weight aluminum alloy you pick will significantly affect both the spreading process and the residential properties of the end product. Due to the fact that of this, you have to make your choice very carefully and take an enlightened technique.
Figuring out one of the most appropriate aluminum alloy for your application will suggest considering a broad array of qualities. These comparative alloy qualities follow the North American Die Casting Association's standards, and we've split them right into 2 categories. The very first group addresses alloy qualities that influence the manufacturing procedure. The 2nd covers attributes affecting the properties of the end product.
How Alcast Company can Save You Time, Stress, and Money.
The alloy you pick for die spreading straight impacts several facets of the spreading process, like just how very easy the alloy is to work with and if it is susceptible to casting issues. Warm fracturing, additionally called solidification splitting, is a common die casting problem for light weight aluminum alloys that can result in interior or surface-level rips or cracks.
Particular aluminum alloys are a lot more vulnerable to warm breaking than others, and your option must consider this. One more usual flaw found in the die casting of light weight aluminum is pass away soldering, which is when the actors stays with the die wall surfaces and makes ejection difficult. It can harm both the cast and the die, so you need to try to find alloys with high anti-soldering residential properties.
Corrosion resistance, which is already a remarkable quality of light weight aluminum, can vary considerably from alloy to alloy and is a necessary characteristic to take into consideration depending on the environmental problems your product will certainly be exposed to (aluminum foundry). Use resistance is another home generally sought in light weight aluminum products and can differentiate some alloys